傳統的錫球技術正在被銅柱技術逐步取代。作為第一道封裝技術,銅柱技術越來越受到歡迎,主要是因為它能應對晶片特徵尺寸縮小、移動設備形態要求以及當前覆晶封裝技術的其他挑戰。與傳統錫球技術相比,銅柱技術在控制連接點直徑和支撐高度方面更具優勢,從而實現更精細的間距。
銅柱技術已證明可實現80微米的間距,並且有望縮小到40微米的間距(圖1)。除了縮小間距之外,銅柱技術還帶來了一些其他優勢,包括改進的電信表面。然而,設計必須在晶片、連接點、底填膠、基板和封蓋等要素中取得平衡,以避免潛在的可靠性問題。
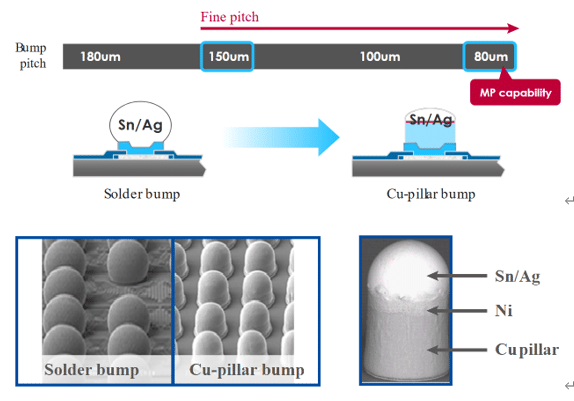
圖1 銅柱技術能將接點的間距縮小到80微米以下,發展潛力巨大 資料來源:智原科技
在覆晶封裝中使用銅柱技術,會對可靠性造成的影響,仍有許多需要研究的地方。每個製造商都採用不同的設計、材料和製程技術,這使得提高可靠性變得具有挑戰性。在比較銅柱與錫球技術,或嘗試將一種銅柱封裝的結果推廣到另一種時,必須非常謹慎,因為連接點設計、材料和製造工藝的多樣性對性能有著重大影響。
銅柱技術的誕生
使用錫球將晶片與封裝基板連接的覆晶封裝技術已經有大約30年的歷史。最近,電鍍銅柱作為晶片與基板之間互連的一部分被引入。在傳統的錫球設計中,錫球構成了晶片與封裝之間的整個電信和機械連接。由於錫球在回焊過程中會熔化,連接結點通常呈現相對球形的形狀,但其直徑和高度的準確性較難控制。銅柱技術能夠創建圓柱形結點,更好地控制晶片底部與封裝基板頂部之間的直徑和支撐高度(圖2)。
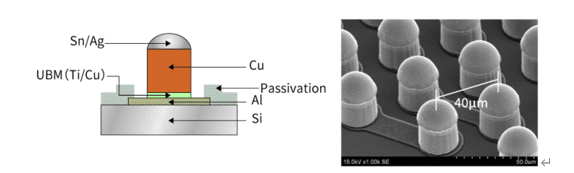
圖2 銅柱結構剖面圖與顯微影像 資料來源:新光電氣工業
銅柱技術於2001年由IBM申請專利,以金屬柱的形式,通過接點連接到晶片和基板的焊墊。到2005年,銅柱技術開始應用於射頻(RF)功率放大器。2006年,英特爾(Intel)在其65nm處理器中使用了銅柱與錫球結點的組合技術。當時,英特爾記錄了銅柱技術的幾個優勢,包括更高的抗電遷移能力、改進的熱導率、簡化的底焊金屬(UBM)和更高的I/O密度。
許多人認為,轉向銅柱覆晶封裝,讓英特爾得以迴避掉一個困擾整個業界的問題–底部填充材料的玻璃轉化溫度(Tg)偏低,因為該公司仍持續在銅柱設計上使用高Tg填充材料。值得注意的是,英特爾並未將熱循環可靠度改善視為以銅柱取代錫球的優勢之一。
銅柱技術自此迅速發展。雖然自2012年以來,覆晶封裝市場的整體增長相對平穩,且未能超越打線封裝技術,但在覆晶封裝領域,銅柱技術的增長非常顯著。除了英特爾(Intel)、德州儀器(TI)等主要IDM業者使用外,銅柱技術也被半導體封裝與測試(OSAT)供應商廣泛採用。
2010年,銅柱技術在覆晶封裝領域的應用占比約為25%,到2015年已超過50%,並且在2018年底占據約75%的市場份額。銅柱技術將成為未來覆晶封裝所使用的主流連接技術。
銅柱技術的優勢
銅柱技術作為第一道連接的主要驅動力在於實現更精細的間距。當間距小於125微米時,錫球技術達到了其極限。覆晶封裝需要回焊連接,這會產生球形或桶形結點。
隨著間距的縮小,支撐高度和結點可靠性會下降,短路風險也會增加。相比之下,銅柱結點在這些方面的限制更小,並且對於支持28nm及以下工藝節點的最新晶片技術是必需的。
銅柱結點的間距範圍從125微米到40微米,目前已在使用或在原型和實驗室研究中得以證明。銅柱技術還能滿足移動設備製造商對更小型化設備的需求,並減少封裝基板層數,從而降低成本。
銅柱技術的可靠性挑戰
雖然銅柱技術提供了顯著的優勢,但要實現可靠的連接點,需要考量許多互相影響的因素。設計特性的平衡必須考慮晶片、連接點、底填膠、基板和封蓋的影響,以避免以下六大問題:
‧晶片連接或填底膠過程中的Low-k介電材料開裂。
‧翹曲可能對封裝共面性和熱界面材料(TIM)產生負面影響。
‧連接點的可靠性,特別是熱循環期間的錫球疲勞。
‧晶片連接過程中的應力,可能導致晶片開裂。
‧第二道連接點的熱疲勞可靠性。
‧因電子遷移導致之故障。
由於這些複雜性,銅柱技術是否比傳統錫球設計更可靠值得探討。答案取決於設計參數的多樣性。不同的晶片、連接、底填膠、基板和封蓋設計平衡方式會對上述問題的嚴重程度產生影響。
設計與製程的變化
銅柱覆晶封裝元件的可靠性,取決於覆晶封裝的整體設計、銅柱接點的設計以及製造它們的材料和工藝。
覆晶封裝設計的差異
自其開發以來,覆晶封裝設計已演變為多種形式,例如裸晶加上底部填充膠、帶蓋封裝(Lid)等。此外,行動應用中越來越多地使用堆疊晶片和堆疊封裝設計,以及通過矽穿孔(TSV)設計。
上述封裝類型都可以使用銅柱或傳統錫球技術。材料和物理設計的差異,可能導致接點、晶片和封裝基板內的機械應力和應變產生顯著變化,並且影響電流集中和熱負載,進而導致電子遷移問題。
銅柱設計的差異
除了封裝材料和設計變異的影響外,銅柱連接點本身在業界內部展現了廣泛的設計變化。其結構在以下方面存在差異:柱的尺寸(高度和直徑)、柱的形狀(方形、橢圓形或圓形)、柱壁(錐形或直形)、柱高度與焊料厚度的比例、柱直徑與凸塊金屬化層(UBM)直徑的比例、柱直徑與鍵合墊直徑的比例,以及是否存在順應層(聚酰亞胺)。
這些接點結構的變異會影響接點和封裝中的機械、熱以及電子遷移應力。封裝和銅柱連接點設計的這些差異使得比較錫球與銅柱的可靠性,甚至比較不同銅柱設備之間的可靠性,變得複雜化。
製程技術的差異
與封裝和連接點設計類似,業界每家公司的封裝組裝製程也有所不同。最常見的製程包括標準回焊(焊膏)、改進回焊(助焊劑浸塗)和熱壓接合。在回焊製程中,矽晶片與封裝基板的對準尤為關鍵。其他製程步驟也必須最佳化,以確保達到可接受的良率和可靠性。
即使是像清潔晶圓焊墊表面這樣簡單的步驟,也必須最佳化,以確保銅柱能正確地與焊墊結合,避免因連接點剪切強度不均勻而影響可靠性。
熱壓接合正迅速成為銅柱封裝組裝的主流製程技術,特別是在間距低於60微米的情況下。該製程僅需2至3秒即可完成,類似於金線接合。然而,從可靠性的角度來看,此製程的一大問題是採用非導電膠(NCP)做為填充材料。
NCP的機械性能與標準填充材料不同,具有較低的彈性模數和較低的Tg。填充材料的性能往往決定了連接點在熱循環過程中的長期可靠性,因此熱壓接合製程需要仔細研究。
儘管銅柱技術有望實現比傳統錫球設計更細的間距,但它也帶來了許多難以解決的問題。可靠性是主要關注點,在材料、設計和製造工藝領域面臨各種挑戰。雖然存在這些複雜性,銅柱預計將很快成為當今覆晶封裝技術中最受歡迎的連接技術。
(本文作者任職於Ansys)