晶振市場格局:日本領先,中國追趕
全球石英晶體元器件廠家主要在日本、美國、臺灣及中國大陸。美國廠商主要針對美國中國及部分專項市場,供求管道較為穩定,產品單位價值較高。日本是國際石英晶體諧振器傳統製造強國。隨著電子資訊行業的飛速發展和智慧應用領域的多元化,日本廠商進一步加大了技術及設備的升級速度,在中高端應用領域實行了排他性的相對技術壟斷,具備較強的規模效應和技術優勢。2013年以後,日本廠商受到原材料和人力資源成本上升,以及全球範圍內其他區域如臺灣、中國大陸等廠商產能擴張等因素的影響,市場份額出現較大幅度下滑。日本廠商將中低端業務逐步轉移至中國,市場份額占比已經由2011 年的59.3%下降到50%以下。
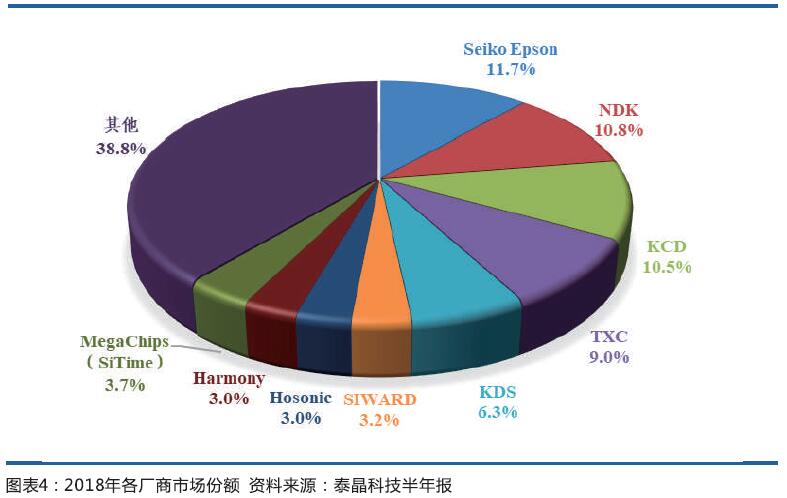
臺灣廠商近年來發展迅速,產品更新速度快,2017年已經佔據了全球約24.3%的市場份額,競爭實力在短時間內也無法撼動。大陸企業起步較晚,核心生產設備依賴外購,產品主要應用於消費類電子和小型電子領域。不過近年來,大陸廠商憑藉成本優勢迅速發展,成長率顯著高於其他國家。根據日本水晶工業協會公佈的資料:2017 年大陸廠商晶振銷售額約占全球的10.10%,較2010年的4.0%增長近6.1個百分點。
替代邏輯一:穩固無源晶振市場份額
無源晶振在對精度要求較低、成本較高的領域廣泛應用。雖然無源晶振的精度、抗雜訊性能、抗干擾性能較有源晶振存在一定差距,但終端廠商在選擇晶振時也會考慮成本因素。無源晶振的價格僅為有源晶振的五分之一至十分之一,在電路中廣泛應用。比如,移動終端的藍牙傳輸、紅外線功能,計時器及鐘錶的計時功能,僅需無源晶振便能實現。
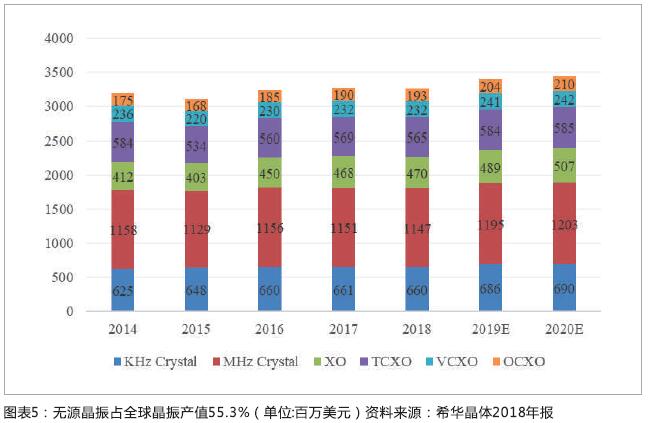
無源晶振產銷量在晶振市場中占較大份額。根據CS&A資料,2018年全球利用石英晶體製成的頻率元件產值為33億美元,其中無源產品產值為18億美元,占比為55.3%。石英晶體頻率元件年銷量180億顆,其中無源產品銷量為164.45億顆,占比為89.3%。根據壓電晶體行業協會(PCAC)的資料,中國市場2016年石英及陶瓷等各類材料製成的無源晶振銷量達到185.7億顆,其中音叉晶體諧振器、微型SMD高頻晶體諧振器的銷量分別為85.1億隻和100.6億隻,銷售額分別為14.6億元和49.3億元。
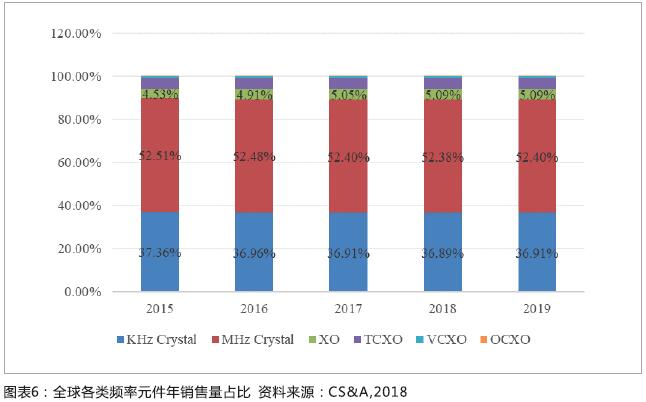
疫情過後中國廠商陸續提價,無源晶振中國國產替代迎來契機。對比四家晶振廠商低頻及高頻晶體諧振器產品參數,日本、臺灣、大陸廠商在無源晶振領域並無明顯差異。目前,中國憑藉勞動力成本、市場規模優勢,已經發展成為無源晶振主要製造基地。2020年新冠疫情導致全球晶振產能減少,供需狀況發生轉變。3月後,中國情勢已經逐步好轉產能釋放在即,晶振行業迎來中國國產替代契機。根據公開資料顯示,泰晶科技等中國晶振企業已於2月20日對產品亦進行新一輪提價,中國廠商在無源領域的優勢將逐步凸顯。
替代邏輯二:TCXO 及TSX訂單增長,中國國產替代空間巨大
經過2017-2018年晶振市場低迷期,部分日企整生合產線。有源晶振可針對晶體的頻率溫度特性做相應的補償,多用於高速通信、導航、汽車電子等領域。2015年-2016年4G建設對溫補晶振需求旺盛,日本各廠商紛紛擴張產線。而2017年後,移動通信行業步入4G到5G過渡階段,溫補晶振需求疲軟,前期擴產導致庫存積壓。日本廠商和全球代理商開始消化庫存,溫補晶振價格一度大幅下跌。石英晶振市場規模在2018年下滑10.11%,至29.4億美元。巨頭NDK公司有源業務在18及19財年連續下滑,KDS業務收入也進入負增長階段。部分小廠商關閉生產線進行整合,實力較強的龍頭企業則專注高附加值產品,市場集中度進一步提升。例如,以京瓷為代表的部分日系晶振廠甚至剝離2520、2016尺寸溫補晶振產線,轉而主攻毛利率更高的1612尺寸產品。
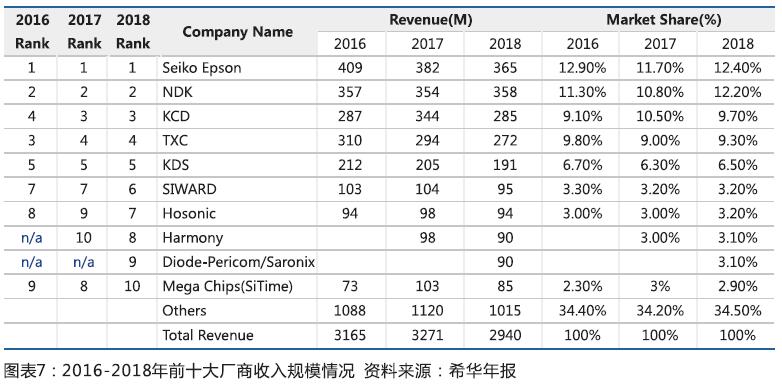
2019下半年有源晶振市場供需情況發生轉變,2520及2016溫補晶振訂單增多。供給端:由於此前部分日本晶振原廠和材料供應商將生產線遷至東南亞等地,導致部分型號產品交貨週期延長,有源晶振又回到供不應求的狀態。需求端:移動通信市場5G基礎設施建設加速,汽車領域配置ADAS等設備的高端車型滲透率提升,綜合導致晶振市場回暖。
5G基站、汽車電子及物聯網等高科技領域對2520(2.5mm*2.0mm)、2016(2.0mm*1.6mm)兩種尺寸的溫補晶振和熱敏晶體需求較高,該型號產品訂單增長,逐步出現量價齊升的態勢。
低成本的熱敏晶體可在一定程度上替代溫補晶振。熱敏晶體和溫補晶振都是在特殊環境下使用的頻率元件,可以改善其頻率溫度補正。熱敏晶體的原理是在普通貼片晶振基礎上增加一顆熱敏電阻以及一顆變容二極體,利用變容二極體的容變功能與熱敏的傳感功能相結合,形成帶有溫度傳感功能的熱敏石英晶振。熱敏晶振在工作過程中受到了溫度感應時可以使晶體產品在工作過程中保持一個精准的不變的溫度,使晶振產品的精度給CPU提供信號的同時又能避免因為溫度的問題給晶振造成頻率較大的偏差。帶有溫度傳感的熱敏晶振是溫補晶振的替代品,其成本低廉、生產快捷,但精度弱于溫補晶振。例如,TCXO溫補晶振的頻率偏差在±0.5ppm 的範圍,晶振給CPU控制中心提供的信號接收到的線路導航精准偏差在3-5米範圍內;而熱敏晶振頻率偏差為±10PPM,導航偏差約為200米。
溫補晶振&熱敏晶體中國國產替代空間巨大,中國企業逐步實現技術突破。惠倫晶體聘請國外具有先進研發經驗和專業學識的高級人才,實現了TCXO器件產品的技術研發,向壓電石英晶體產品全系列發展。泰晶科技也研發出廣泛應用於移動通信和汽車電子領域的2520、2016兩種型號熱敏晶體。對比日本、臺灣、大陸五家公司產品資料,大陸企業將逐步突破熱敏晶體和溫補晶振技術,進一步縮小和日、台企業的差距。
替代邏輯三:突破光刻技術,推進小型化、高精度發展
(1)MEMS技術可解決傳統機械加工的局限
高穩定性的晶體元器件晶體單元/晶體振盪器按照切型主要分為三種:(1)kHz級的晶體單元採用音叉型結構振動子;(2)MHz級的晶體單元採用AT型結構振動子;(3)百MHz超高頻晶體單元採用SAW型振動子,溫度特性曲線和音叉型振動子類似。隨著下游產品對晶振抗振性、相位雜訊等、尺寸小型化等參數要求越來越高,傳統機械加工的局限性逐漸顯露。
音叉型晶振缺陷:單元尺寸壓縮後將難於取得良好的振盪特性。當石英振動子的尺寸從1.2×1.0mm減小到1.0×0.8mm時,串聯電阻值(CI值)會升高30%左右,也就是說音叉型晶體單元尺寸壓縮後將難於取得良好的振盪特性。
AT切型晶振缺陷:傳統機械加工難以滿足嚴格的公差要求。AT切割是目前使用最廣泛的石英晶體類型之一,常用於高頻晶振。典型的超小型胚料尺寸小於3.5*0.63mm,加工難度大幅增加。大規模生產小型晶體時,需要將公差控制在2um以內,而傳統機械加工難以滿足嚴格的公差要求。
超高頻晶振缺陷:多次倍頻導致相噪損失嚴重。晶振工作頻率通常與晶片厚度成反比,傳統機械加工最適合的頻率範圍為1-40MHz(對應晶片厚度0.04mm)。以傳統方式生產百MHz晶振需要將晶片加工至超薄,從而導致出現穩定性差及易破損的缺點。因此,生產百兆赫茲高頻晶振通常採用10MHz 成熟產品作為基準頻率源,並經過多次倍頻獲得所需信號。但這樣導致電路複雜,相噪損失嚴重。
微電子機械系統(MEMS)技術的有效應用為石英晶體的加工提供了技術借鑒和啟發。MEMS技術利用IC加工技術實現微納米尺度加工,在加工精度、加工手段、EDA(電腦輔助設計)等方面具有先天優勢,因此石英晶體技術與MEMS技術的結合成為必然趨勢。
音叉諧振器包括底部和從底部延伸的兩個振動臂,在兩個振動臂上鍍有激勵電極(紅色部分)。該常規結構的晶片微型化後,激勵電極面積將隨之減小,不利於起振。MEMS技術通過對振動片進行三維立體加工形成H型槽的構造,既確保了電極的面積,又提高了電解效率。MEMS技術有效推動晶體諧振器小型化發展,光刻加工下的晶振體積縮小至18.8mm3小型音叉型晶體器件,體積僅為原有產品1/10以下。
(3)MEMS技術用於AT型晶體/AT振盪器,將尺寸公差保持在1um以內
利用MEMS技術的光刻加工可以提升石英晶體晶片的一致性與穩定性,光蝕刻工藝能夠將尺寸公差保持在1um以內。
光刻工藝首先使用電子束真空沉積系統將石英晶片化學蝕刻至預定頻率,清潔並用鉻和金薄膜金屬化。石英掩模和雙對準器光刻生成AT條帶圖案,其中晶片的頂部和底部表面同時對準和曝光。然後通過隨後的光掩模步驟限定晶體電極和探針焊盤案。然後對晶片進行化學金屬和石英蝕刻以形成單獨的AT條帶。最後,使用孔掩模和薄膜金屬沉積將頂部和底部安裝墊連接在一起。光刻工藝完成後,晶圓包含上百個獨立的超小型AT晶體諧振器。
(4)MEMS技術用於HFF晶體單元/HFF振盪器,使高頻產品可以直接以基波起振
不同于傳統機械加工將晶片整體變薄,光刻加工僅減少驅動電極附近的厚度(反向台構造),保持晶片強度。這樣以來,百MHz的高頻晶振可以直接以基波起振,不用以中低頻成熟產品作為基準頻率源。光刻加工的HFF振盪器具有優良的抗震性以及較低的相位雜訊,適用於光傳輸裝置、基站等通信基礎設置。
(5)中國國產企業突破光刻技術,推進產品向小型化、高精度趨勢發展
石英晶體硬度及理化性質穩定,頻率基本不隨溫度變化,由此產生的內部振盪損失也最小,非常適合精密製造。同時,區別于傳統的機械式加工生產方式,改良的制程更便於批量生產,可以在保證小型化的同時把偏差控制在最小限度內,從而使產品具備小型化、低耗電、高穩定、高頻率的優勢。應用MEMS技術的微型化產品與傳統機械加工生產的晶振前端工藝區別為:1)微型化產品切割環節不是一次性切割成為單個音叉晶體單元,而是首先切割成可以集合上千支晶片單元的大方片;2)音叉晶片及電極成型環節採用雙面光刻工藝,在WAFER片上進行光刻、金屬蒸鍍、鐳射調頻等集成處理,單個音叉單元尺寸極小。
中國國產企業光刻技術已取得突破。泰晶科技從2011年開始佈局光刻工藝研發,2014年組建了中國同行業首家微納米晶體加工技術重點實驗室,以鐳射調頻和光刻技術為基礎,加強MEMS技術在晶體諧振器產品的應用。目前公司已經取得了微型晶體諧振器生產的核心技術研究成果,成功使用雙面光刻工藝,將超過3000顆的“1610”型號晶體諧振器集成至3寸的WAFER 片上。